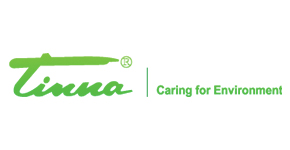
Tinna Rubber and Infrastructure Ltd
HI TENSILE RECLAIM RUBBER
Producing reclaim rubber is the most traditional way of recycling waste tyres. Unfortunately in the conventional process, the rubber molecules are cut to smaller length by oxidation which causes sharp drop in tensile strength and fall in abrasion properties. This process also causes pollution by emitting effluent waste and obnoxious gasses.
We, at Tinna, follow the latest environmental friendly technology which does not use steam thereby neither producing any effluent nor releasing any foul smell in the atmosphere. In this latest mechanical process, the tensile is retained at a much higher value. Compared with the conventional reclaim having a tensile of 3.5-4.5 mpa, the new technology makes reclaim of 7-10 mpa tensile.
We also manufacture compounded reclaim having a tensile of 13-15 mpa. This pre compounded reclaim can be used in a variety of rubber products without incorporating carbon black. This is a great advantage to rubber factories as the use of carbon black makes the rubber factory and its surroundings extremely dirty and by using compounded reclaim, the use of carbon black is eliminated. The cost advantage of reclaim is very high as power consumption, labor and machinery utilization goes down tremendously.
ULTRA FINE HIGH STRUCTURE TYRE CRUMB
We, at Tinna, produce ultra-fine hi structure crumb of 80-100 mesh from Radial Trucks and Buses tyres. In the process, the steel wires are removed using a number of magnets. The thin wires are crushed and these wires cut through the crumb rubber giving it roughness and perforation creating a very high surface area. During the compounding, the rubber penetrates into these hi structure particles and a strong mechanical bond is created.When mixed in a rubber compound, this crumb becomes one with it and imparts high properties. IRMRA has concluded in its study that as the particle size of crumb reduces, it gives higher physical properties. It was also found that by using 10 phr of 80/ 100 mesh crumbs, no loss of properties was observed, even though the carbon phr had to be reduced to maintain the hardness, thus affecting cost reduction without impairing properties.
Generally 2/3 phr of fine crumb were used to improve mould flow of complicated designs like tyre tread. A detailed study was done by IRMRA using Tinna crumb, result of which shows that up to 15 phr of crumb rubber used in a standard tyre tread compound having tensile strength of 26 mpa and E.B -580%, Abrasion index of 107, does not affect these properties significantly.
A detailed study was done in USA in association with the largest tyre companies confirming the use of 80-100 mesh crumb in new tyres. To get the best results, crumb has to be mixed with the rubber in the initial stage before adding other fillers so that the crumb penetrates into the high structure of the crumb.
The problem with 30-40 mesh conventional crumb in a rubber compound is that it is just a foreign matter and a filler which does not bond with the new vulcanizate. When a rubber product is put to use this crumb detaches itself if used in large quantities.